In downtown Valparaiso, a historic government building that’s currently Porter County’s 911 Central Communications Center (formerly the Porter County Jail) was showing signs of water infiltration and masonry deterioration. Our team was brought in to assess the damage and execute a focused façade restoration. The building's location, age, and previous repairs all pointed to one core issue: failed water management at the window heads.
Pre-Construction Observations: Signs of Systemic Failure
From the very start, site conditions revealed several examples of what happens when critical envelope details fail:
- A previous flashing repair had failed. Installation errors included loose fasteners, improperly sealed terminations, and missing components.
- Corroding steel lintels, concealed behind the façade but exposed after brick removal.
- Cracking and detachment of perimeter sealants at window frames.
These deficiencies, captured in field photos before and during work, clearly showed how water had been entering the wall system and putting long-term durability at risk.
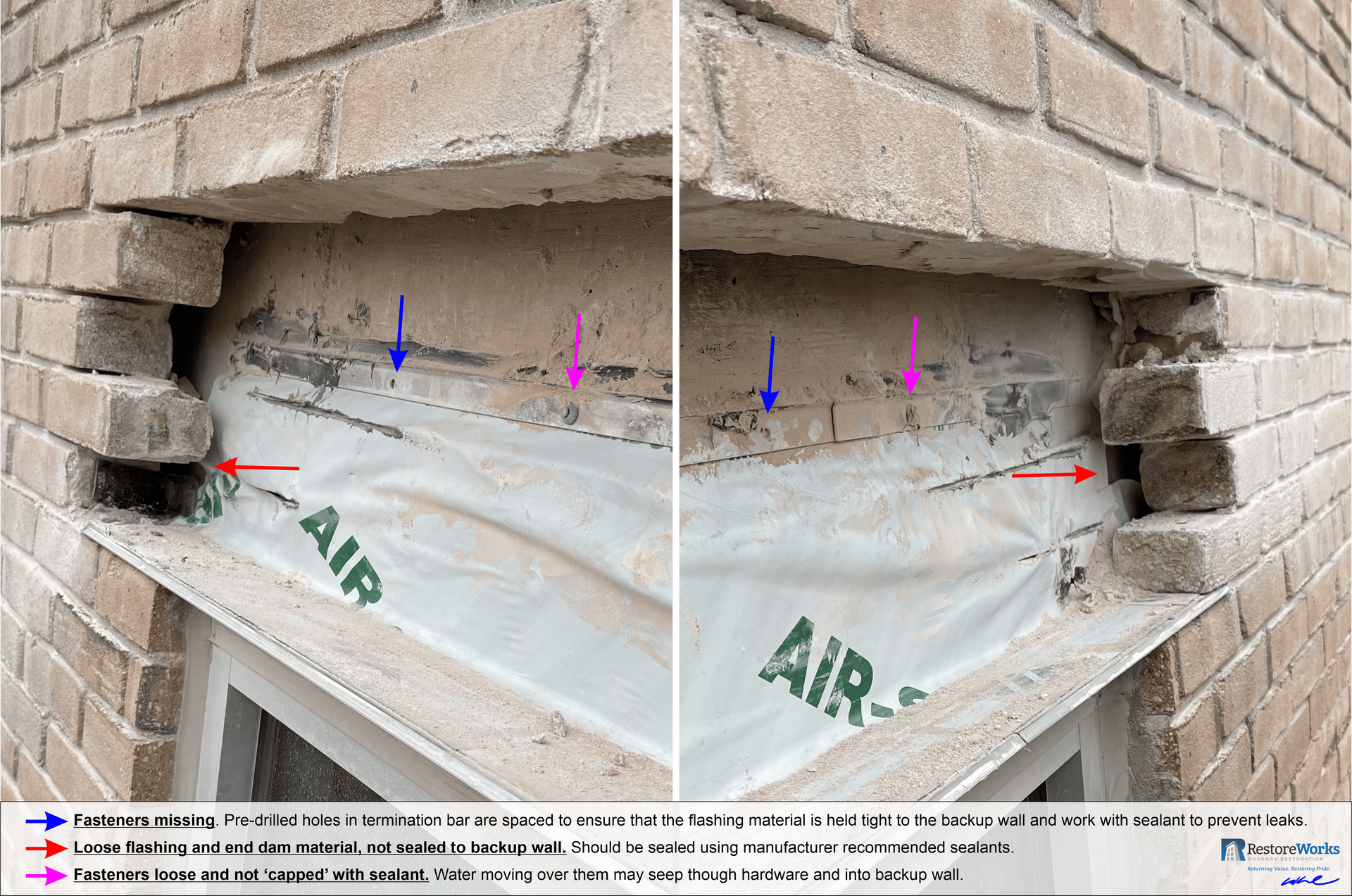
What We Did: Restoring Lintels, Flashing, and Façade Integrity
The project focused on 39 window and door openings on the building’s east wing. We addressed 36 window lintels and three door lintels (346 linear feet total) with the following scope:
1. Steel Lintel Preparation
- Brick was removed in 4-course heights to expose the lintels.
- Rust and loose material were wire-brushed or ground off as needed.
- We prepped all existing steel, removed loose/flaking rust, cleaned with denatured alcohol, and then painted with a zinc-rich primer to prevent future corrosion.
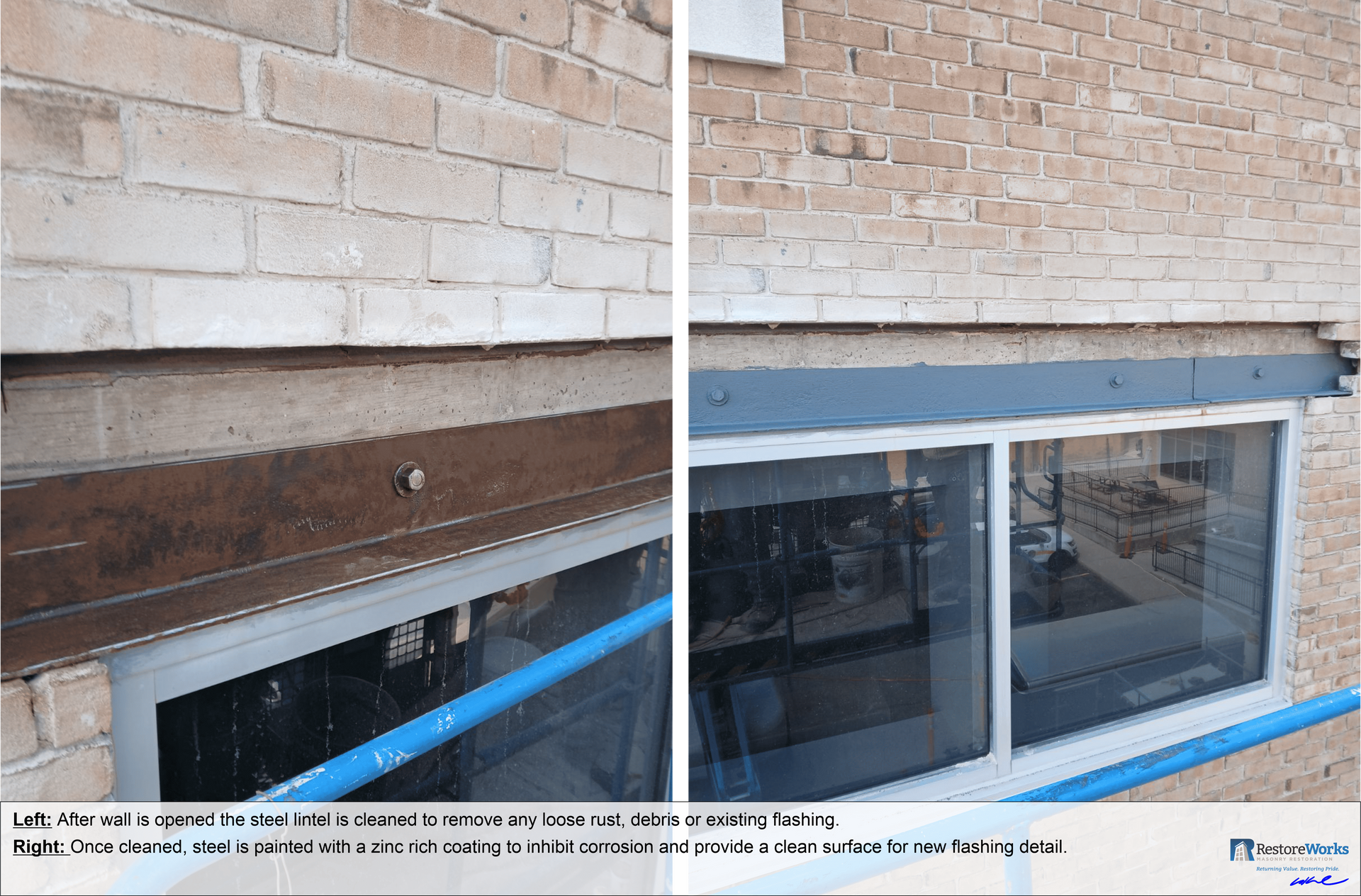
2. Flashing System Installation
We installed TotalFlash Panels by Keene Building Products, a pre-assembled system that includes:
- EPDM flashing membrane
- Stainless steel drip edge
- Integral weeps and preformed rubber end dams (39 left/right pairs)
- PVC termination bar
- BTL-1 Butyl Sealant (100+ tubes used) for adhesion and air/moisture sealing
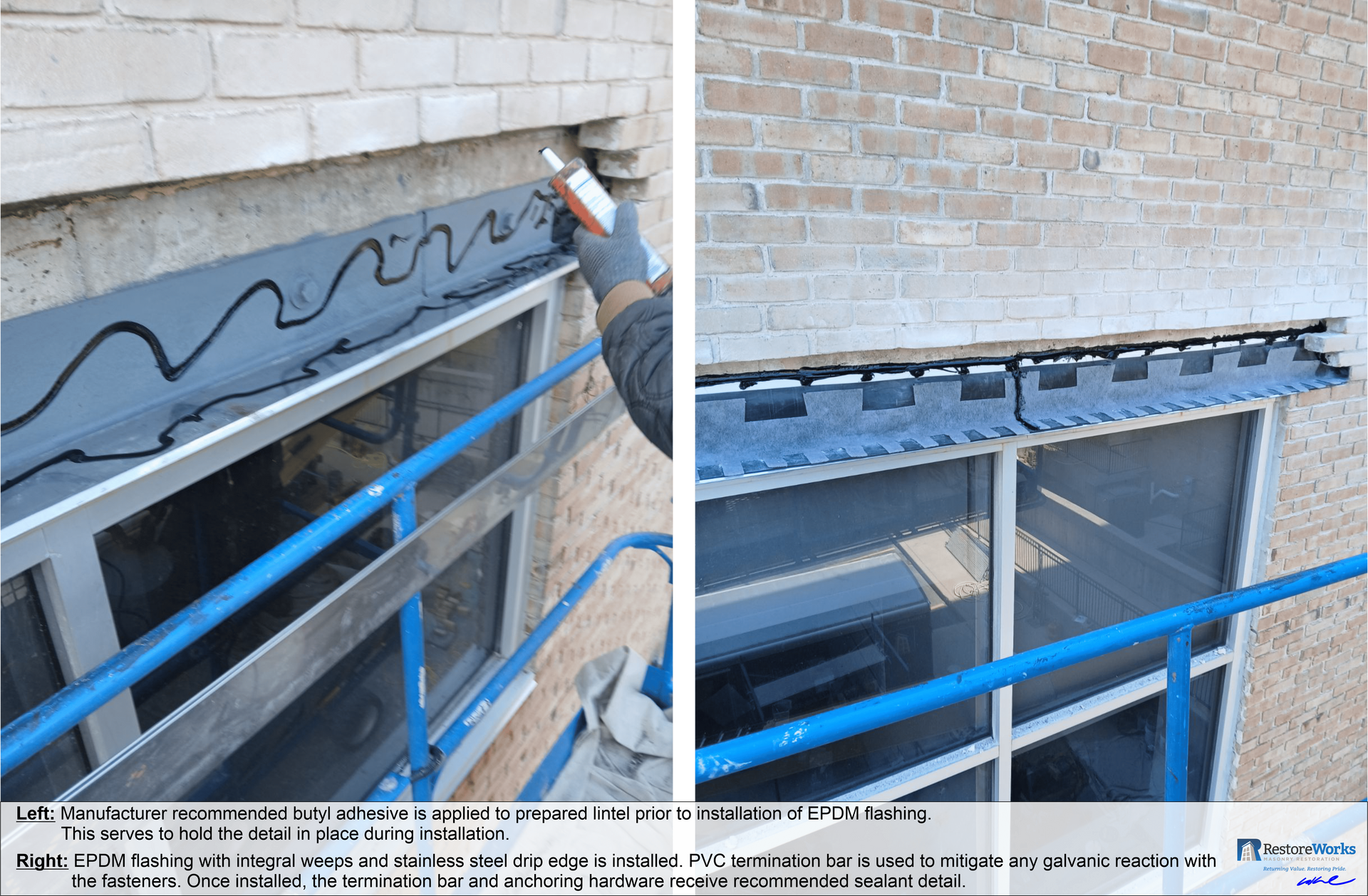
3. Masonry Reconstruction
- Salvaged brick was reset to match original layout.
- Sourced matching brick to replace any damaged ones. (Via Crown Brick)
- Joints were repointed using SpecMix MC-04 and cleaned using Prosoco 600, a proven masonry detergent.
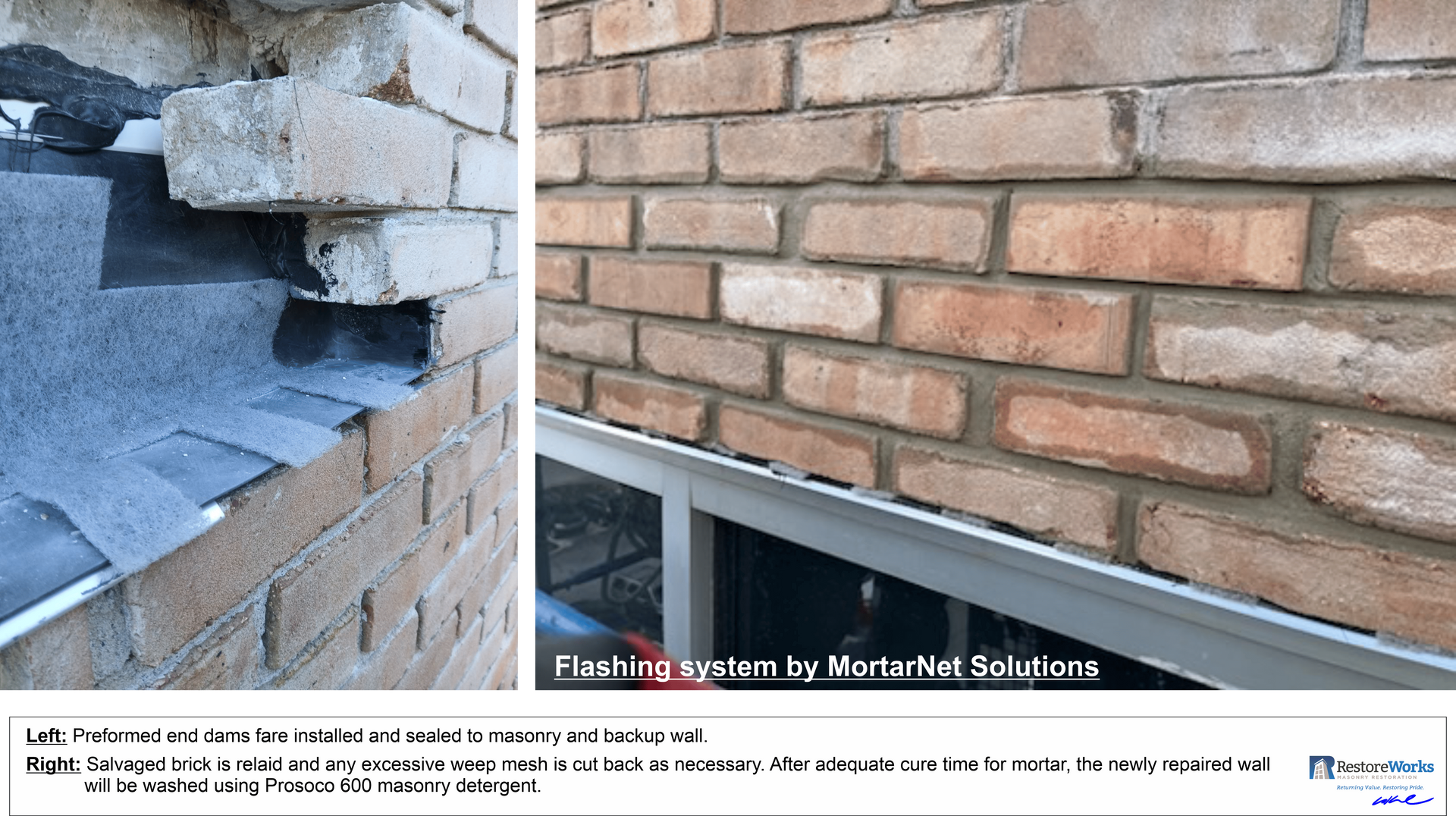
4. Sealant Replacement
- Over 663 linear feet of perimeter sealant was removed and replaced using DOWSIL 795 silicone in gray.
- While performing the work, we identified two failing masonry control joints and replaced them at no additional cost.
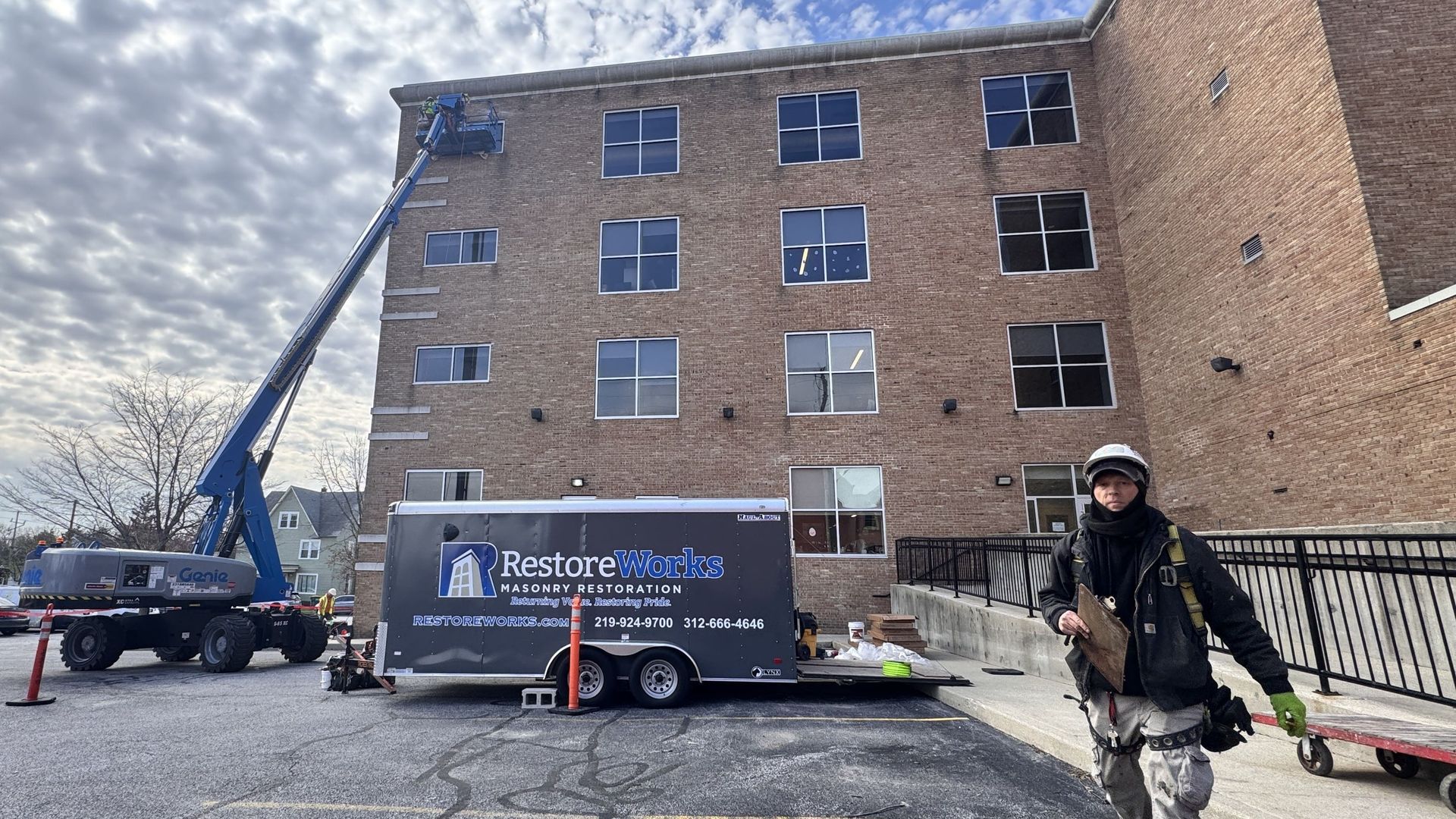
Project Impact
This was a textbook example of what happens when a building’s water control layers are compromised, and how targeted building envelope restoration can solve the problem without full replacement or major disruption.
The work restored drainage functionality, protected structural components, and preserved the original look of a historically significant building still in civic use.
Material Highlights
System/Material | Application | Supplier |
---|---|---|
TotalFlash Panels | Integrated flashing system | Keene Building Products |
BTL-1 Butyl Sealant | Flashing adhesion and air sealing | Keene Building Products |
DOWSIL 795 Silicone | Window and door perimeter sealant | Dow |
Prosoco 600 | Final masonry cleaning | Prosoco |
SpecMix MC-04 | Brick was rebuilt | SpecMix |
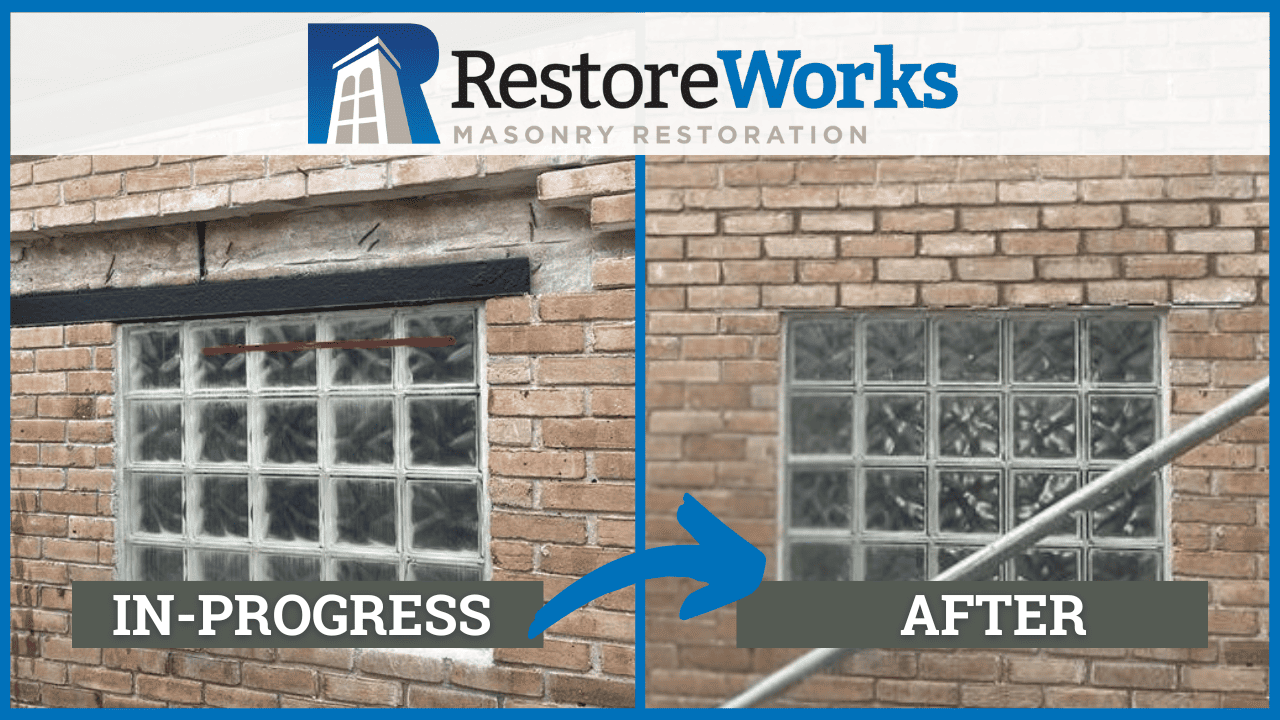
Looking Ahead
Restoration work like this is becoming more common across Valparaiso, Porter County, and Northwest Indiana, especially as older buildings transition to new uses. By correcting failed detailing from past repairs and installing proven systems from trusted manufacturers like Keene Building Products, we helped make sure this building’s next chapter is built on a solid foundation.
Beyond performance, the products by Keene Building Products streamlined the entire restoration process. With everything included on a single submittal sheet (membranes, drip edges, end dams, termination bars, and compatible sealants), the system was easy to order, install, and use in the field. That simplicity helped our team maintain consistency across all openings and meet project deadlines without delays or product coordination issues.