Pressure washing is a key part of maintaining a commercial building’s exterior, but improper methods can lead to costly damage, especially when dealing with masonry, concrete facades, and balconies. If you're managing a high-rise, a historic structure, or a modern office building, here are five essential considerations before starting any pressure washing project.
1. Know Your Surface Material
Different materials require different cleaning approaches. Commercial concrete facade restoration and masonry restoration projects often involve delicate surfaces that can be damaged by high-pressure water.
- Brick and limestone are porous and can degrade if water pressure is too high.
- Concrete can withstand higher pressure but requires careful attention to avoid exposing aggregate or causing surface wear.
- Painted surfaces may chip or fade if the pressure is excessive.
According to the National Park Service, “most chemical cleaning methods involve water [and] have many of the potential problems of plain water cleaning,” including the risk of moisture intrusion that can worsen masonry deterioration.
Before proceeding, consult a masonry expert to assess the condition of your building materials and determine the appropriate cleaning method.
2. Choose the Right Pressure and Cleaning Agents
Not all pressure washing techniques are the same. Using the wrong pressure setting or chemical solution can cause damage or leave behind stains. For restorative masonry cleaning, consider:
- Soft washing techniques that use lower pressure with specialized cleaning solutions.
- Environmentally safe detergents to remove biological growth like algae, mold, or efflorescence without harming the masonry.
- Testing a small area before full-scale cleaning to gauge the impact on the surface.
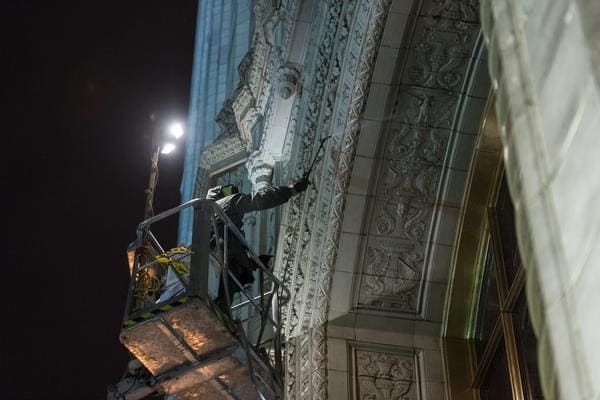
3. Address Existing Masonry or Concrete Issues First
Pressure washing will not fix structural problems. In fact, it can make them worse. Before cleaning, inspect the building for:
- Concrete balcony repair needs, such as cracks, spalling, or exposed rebar.
- Masonry lintel repair requirements, as lintels often accumulate moisture and may deteriorate faster.
- Signs of deteriorating mortar joints, which should be repointed before applying pressurized water.
Ignoring these issues can lead to accelerated deterioration, water infiltration, or even structural compromise.
4. Consider the Impact of Water Runoff and Environmental Regulations
In urban environments like Chicago, water runoff from pressure washing is often regulated. Many cities require wastewater containment, especially when chemicals are used. Consider:
- Proper drainage to prevent water pooling near the foundation.
- Using water reclamation systems to prevent contaminants from entering storm drains.
- Checking local regulations to avoid fines related to improper disposal of cleaning solutions.
A professional contractor familiar with regulations can ensure compliance with environmental guidelines while maintaining your building’s integrity.
5. Hire a Professional Masonry Restoration Contractor
While DIY pressure washing might seem cost-effective, improper techniques can lead to expensive damage. A qualified contractor specializing in commercial masonry restoration services will:
- Use industry-approved methods tailored to your building’s material and condition.
- Identify underlying masonry issues before cleaning.
- Ensure compliance with local building and environmental regulations.
Get Expert Help Before You Pressure Wash
Before pressure washing your commercial building, make sure you’re taking the right approach. Improper cleaning can cause irreversible damage, leading to costly repairs. RestoreWorks can help assess your building’s needs and recommend the safest and most effective cleaning methods.
Contact us today for a consultation and let’s protect your investment with the right approach to masonry and concrete restoration.